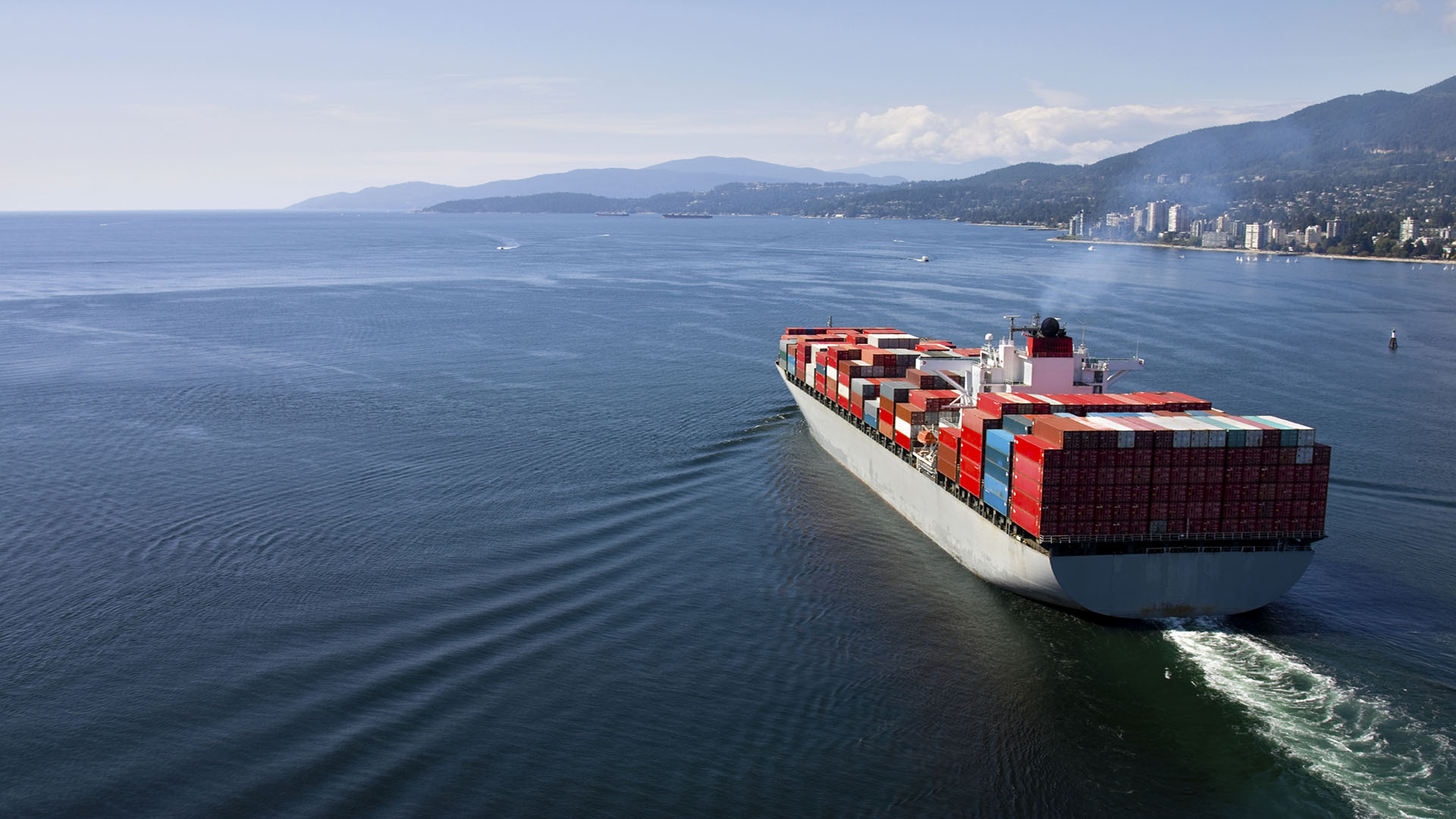
Carriage of Direct Reduced Iron (DRI)
Introduction
Direct reduced iron (DRI) in various forms is described in the International Maritime Sold Bulk Cargo (IMSBC) Code, (hereinafter, the Code). The latest addition, which becomes a mandatory part of the Code from January 2025, is the entry for the Type D, by-product fines with a moisture content of at least 2%. This entry runs over multiple pages and contains large amount of important information and guidance. In this Circular, the main points of the Type D entry are summarised, and, where appropriate, additional guidance and observational notes have been added.
This Circular has been prepared for the International Group of P&I Clubs (IG) in conjunction with Dr J H Burgoyne & Partners LLP (Burgoynes’) with input from INTERCARGO. Explanatory notes provided by Burgoynes are included in blue text within the body of this Circular.
It should be noted that this Circular is for guidance only and the relevant entries from the IMSBC Code, which are appended to this Circular, remain the primary source of carriage requirements which should be relied upon.
Background
Direct reduced iron (DRI) is formed by passing hot reducing gases, such as hydrogen, methane and carbon monoxide, over iron ore, which is usually in the form of lumps or pellets. This produces a highly porous iron material which has a very large internal surface area available for re-oxidation. The principal hazards associated with DRI are its ability to undergo self-heating through oxidation and its ability to generate hydrogen from reaction with water/moisture. When stowed within the confines of a cargo hold, hydrogen produced by reaction with water can form an explosive atmosphere inside the hold, presenting a risk of explosion.
The principal forms of DRI are Type A (hot-moulded briquettes) and Type B (pellets), but fines are also generated during manufacture and handling (via abrasion) and from filtering particles out of off-gases. Fines are not generally suitable for inclusion with Types A and B, so these are screened out and handled separately.
Formerly, fines would be shipped under DRI Type C, but the IMSBC Code entry for this type defines the moisture level of the cargo as not exceeding 0.3%. That low moisture level is often not feasible due to handling practices for fines, such as outdoor storage and handling being subject to rain.
In addition, the Code calls for DRI (C) cargoes to be shipped under inert gas, as for DRI (B). Inert gas is intended to exclude air (oxygen), thus limiting self-heating due to reaction with oxygen. However, as set out below, self-heating is typically not the main issue with fines. Instead, the prevalent risk is the generation of flammable hydrogen gas due to reaction with water, leading to a scenario where the holds need to be ventilated in order to maintain low hydrogen concentrations, below the lower explosive limit plus a margin of safety.
With the production of DRI(C) fines having a moisture content not exceeding 0.3% being difficult to achieve, in the IG Clubs’ experience shippers often sought to ship such cargoes under exemptions in accordance with section 1.5 of the IMSBC Code. Those exemptions often sought to avoid shipment under inert gas, instead using mechanical ventilation as an alternative arrangement, but this proved difficult due to the need for tripartite agreement. Therefore there was a need for the industry to work collectively to seek a more permanent, but safe, long-term solution.
Accordingly, Amendment 07-23 to the Code introduces a fourth DRI schedule: DIRECT REDUCED IRON (D) (By-product fines with a moisture content of at least 2%).
Like DRI (C), DRI (D) is described as a by-product of the manufacturing and handling process of DRI (A) and DRI (B), but has a higher moisture content (≥2% as compared to ≤0.3% for DRI (C)).
There is also reference in the new DRI (D) schedule to the risk of liquefaction if shipped with a moisture content exceeding its transportable moisture limit (TML). DRI (D) is therefore classified as both a Group A and Group B cargo.
The principal hazard associated with DRI (D) fines is the generation of hydrogen, due to the relatively high moisture content and reaction with water. By contrast, the dense packing of the fines often reduces oxygen/air ingress into the bulk, with the result that the propensity for self-heating through atmospheric oxidation reactions is reduced, often to non-problematic levels. As such, there is no requirement in the DRI (D) schedule for purging the cargo hold with inert gas to prevent an explosive atmosphere from forming, nor in keeping the cargo hold tightly sealed to exclude oxygen ingress, whereas there are such requirements for DRI (B) and DRI (C). Instead, a regime of controlled mechanical surface ventilation and regular gas concentration measurements should be introduced in order to keep the hydrogen concentration within the holds below a designated limit.
The IG has previously issued Circulars on DRI cargoes due to a number of incidents some of which have resulted in fatalities. Whilst these advisories were issued nearly two decades ago, given the seriousness of those casualties and a cargo that potentially emits hydrogen, the IG has supported independent expert input to the International Maritime Organisation on the drafting of revised DRI schedules, including this latest one for DRI (D).
Hazards of DRI (D)
The entry for DRI (D) leads with a reference to a potential temperature increase when the material is handled in bulk; and the risk of overheating, fire and explosion due to the reactivity of the cargo with air and water to produce hydrogen gas and heat.
Whilst DRI (D) will react with oxygen and generate heat, its dense packing and the very small spaces between particles are often such that oxygen/fresh air is not able to diffuse into and through the stow to the same extent as with other types of DRI types, particularly the larger briquette/pellet forms. This low permeability means that self-heating is considered a secondary hazard. The primary hazard observed is hydrogen generation, due to the reaction between the DRI and water / moisture. The focus of the new DRI (D) schedule is on the measurement and control of the hydrogen gas concentrations in the ullage spaces.
Although self-heating is considered a secondary hazard, the reaction with air can lead to oxygen depletion in the cargo spaces, and possibly also adjacent spaces, where flammable gases (i.e. hydrogen) might also accumulate. The Code therefore stipulates that no person shall enter a loaded cargo space (or enclosed adjacent space) unless such space has been ventilated and found to be gas-free.
The Code refers here to the Revised recommendations for entering enclosed spaces about ships (Resolution A.1050(27)).
DRI (D) cargoes are liable to liquefaction if shipped at a moisture content in excess of its Transportable Moisture Limit, and is therefore classified as a Group A cargo in the Code in addition to the Group B designation due to its reactivity hazard.
The dust produced during handling of DRI (D) can be hazardous to health (irritation to the respiratory system and/or damage to the eyes).
Preparation of cargo and loading
Holds
As for other DRI cargoes, cargo spaces being prepared for carriage of DRI (D) should be clean, dry and free of salt and residues of previous cargoes. Wooden battens, loose dunnage, debris and other combustible materials shall be removed.
The specific reference to salt is because the reaction between DRI and water is more vigorous in the presence of salt than without (in other words, DRI is much more reactive with sea water than with fresh water).
Cargo ageing
For material being prepared for loading, outdoor stockpiles are permitted, provided that the stockpiles are arranged to promote exposure to the atmosphere and thus facilitate natural ageing.
This “ageing” is the process by which the most active sites on the external and internal surface of the particles react with atmospheric oxygen and thus become “passivated” against further reaction during carriage.
The cargo should be aged in this way for at least 30 days prior to loading, and the shipper is expected to provide the Master with a certificate issued by a competent person (who is recognised by the competent authority of the port of loading) stating that the cargo has been prepared and aged appropriately (i.e. naturally aged for at least 30 days).
The shipper shall also provide the Master with a certificate issued by a competent person (again recognised by the competent authority of the port of loading) stating that the cargo does not meet the criteria for class 4.2 materials (i.e. it is not liable to self-heat).
This is effectively declaring that the cargo does not behave like, say, DRI (B), which can self-heat problematically.
Moisture
Whilst outdoor storage is permitted, the risk of liquefaction means that the moisture content should be kept below its TML during loading operations. This means that the cargo should not be handled in the rain and that non-working hatches are kept closed. Discharge in the rain is permitted as long as the total cargo package in a given hold is to be discharged at that port.
The TML for DRI fines is typically between 9-12% [see the IIMA publication, ‘Direct Reduced Iron By-Product Fines (DRI D): A Guide to Handling, Storage & Shipping’ found on the IIMA website- www.metallics.org].
Once discharged ashore into the open air, the potentially hazardous consequences of hydrogen production and liquefaction no longer apply.
Temperature
DRI at elevated temperatures should not be loaded, the threshold temperature being 65 °C with measurements being taken at the stock pile over three consecutive days prior to loading. Measurements are to be taken 20-30 cm beneath the surface at 3m intervals throughout the stockpile. Temperatures shall also be measured during loading, with a log detailing the temperature of each lot being recorded, and with a copy being provided to the Master. Once loaded, thermocouples are placed into the stow for the cargo temperature to be monitored remotely, without entering the holds.
The measurement of temperatures in this way might be limited due to the high degree of thermal insulation offered by the cargo, which can mean that measurements in isolated points throughout the hold might not be representative of the bulk conditions of the stow. Also, localised heating ‘hot spots’ in areas of the stow away from the thermocouple positions might be missed. That said, a network of thermocouples placed within the stow is preferable to single measurements from bilge sounding pipes or “temperature” sounding pipes, which are usually at only one or two places per hold and are therefore not representative.
Hatch cover closing
Weather permitting, hatch covers shall be left open after completion of loading to allow cooling of the cargo, stabilisation of cargo temperature and natural ventilation of the hold.
This seems to be contrary to the current advice to keep non-working hatches closed, see above. The intention appears to be that the closure of non-working hatches is to protect the cargo against being wetted by rain (if applicable), but once loading is complete, and if there is an opportunity to do so (i.e. a period of dry weather), then the hatch covers should be kept open to assist with heat dissipation and natural ventilation.
Once loading has been completed and the hatch covers are closed, the Code calls for the ship to wait for at least 24 hours before sailing to ensure that the cargo temperatures are stable and do not exceed 65 °C, and that the concentration of hydrogen in the ullages has stabilised and does not exceed 1% by volume for at least 12 consecutive hours.
Hydrogen is a flammable gas; the minimum concentration of hydrogen that is needed to form a flammable mixture with air is 4% by volume. This is the “lower explosivity limit” or LEL. Therefore, the 1% by volume mentioned here represents a quarter of the LEL (25% LEL). Not exceeding 1% by volume gives a safety margin between this ‘action level’ and 4% by volume, which is the lowest hydrogen concentration in air at which an explosion could occur.
Certification
Prior to sailing, a further certificate shall be issued by a competent person (once again recognised by the competent authority of the port of loading), stating that the proportion of material larger than 12mm in diameter is no more than 3% by weight, that the moisture content is at least 2% and below the TML, and that the temperature of the cargo loaded does not exceed 65 °C.
This section of the Code therefore calls for three certificates to be provided by the shipper stating that the cargo:
- Does not meet the criteria as a class 4.2 material;
- (ii) Has been appropriately aged; and
- Has proportions of large particles, moisture content and temperature below the specified limits.
In addition, the Master is to be provided by the shipper with the temperature log of the cargo during loading.
Carriage & cargo management
General precautions
As noted above the primary hazard associated with the carriage of DRI (D) is the generation of hydrogen, a flammable gas, within the ullage spaces of the hold. Unlike other DRI cargo types, the entry for Type D makes reference to a risk assessment to be undertaken in advance of the voyage and which is based on the “comprehensive information on the risk of hydrogen generation and the factors which might affect the rate thereof”, to be provided by the Shipper.
This risk assessment might include other factors such as the weather conditions expected en route, the speed of the ship and distance to the discharge port, the availability of ports of refuge along the way, and any information on hydrogen evolution that might be available. The Master, with the aid of the shipper, should also ensure that the crew are properly briefed on the risks involved prior to loading commencement.
The ship should be equipped with the means to take measurements of the concentrations of hydrogen and oxygen. This is achieved using a suitably configured gas detector fitted with a pump and length of hose which can be inserted into the gas sampling points of each cargo hold.
In practice, and as recommended by the Code, the measurement of hold gases and cargo temperatures might typically be undertaken by an experienced cargo technician appointed by the Shipper. The Code recommends that the technician is present during loading and throughout the voyage.
The Code calls for such measurement devices to be suitable for use in an oxygen-depleted atmosphere. This is because some types of combustible gas analysers (“catalytic bead sensors”), which are sensitive to hydrogen, require a minimum level of oxygen in order to operate correctly. In oxygen-depleted atmospheres, as is often found with DRI cargoes, catalytic bead sensors might not provide reliable results. Similarly, some other types of combustible gas sensor that can operate in low oxygen environments are blind to hydrogen. The selection of appropriate sensor equipment is therefore extremely important for all DRI cargoes.
Ventilation
The Code sets out that mechanical surface ventilation shall be provided in each hold to maintain the hydrogen concentration less than 1% by volume (25% LEL).
Given the risk of flammable atmospheres being present, only fans which are suitable for use in explosive environments should be used for mechanical ventilation. It is also important that the ventilation applied is surface ventilation, and that fresh air is not introduced into the stow itself (through fan ducts lower down in the hold, for example) as this could encourage oxidation reactions in the bulk, leading to an increase in the heat being generated due to and an increase in the rate of reaction.
Ventilation should be limited to the time required to remove any hydrogen gas accumulations to below 1% by volume, in order to minimise the risk of fresh air/oxygen being introduced into the cargo. The length of time and frequency that ventilation is applied will be derived to some extent by prior experience, and in this respect the Code introduces the concept of a time-based gas prediction curve, the results of which should be used to update the voyage risk assessment.
The time-based gas prediction curve is a tool for understanding the likely rate of hydrogen evolution. It is a graphical representation of how the hydrogen evolution occurs over time, and it is constructed by measuring the hydrogen concentration in the ullage of each hold after ventilation has reduced the concentration to <0.2% by volume (i.e. to below 5% LEL), and plotting this data against time. With mechanical ventilation stopped and natural vents closed, measurements are taken every 2 hours over the course of the next 24 hours, or until the hydrogen concentration exceeds 1% by volume, whichever occurs first. The data are then used to estimate the time required to reach a hydrogen concentration of 1% by volume in the absence of ventilation, and this time period can then be used to optimise the ventilation schedule. It is also useful to understand how quickly hydrogen gas might accumulate within a hold during periods of heavy weather, when it might not be possible to apply ventilation. All of this information is then fed into the risk assessment process.
Expert assistance might be required to analyse the gas concentration data and to derive an appropriate ventilation regime.
Mechanical ventilation shall be by extraction, rather than blowing in air from the outside, with exhaust ducts removing the expelled gases to a safe location (e.g. away from the accommodation). Two spare sets of ventilation equipment shall be available on board, and the crew or other authorised persons shall be familiar with its installation, operation and maintenance. The Code sets out minimum airflows of 1.2 m3 per hour per tonne of cargo.
Emergency procedures
If the hydrogen concentration is approaching or exceeds 1% by volume, then the hold(s) in question shall be ventilated (via mechanical and/or natural surface ventilation) until the concentration falls to or below 0.2% by volume. The hydrogen concentration should be measured more frequently if it exceeds 1% by volume (preferably hourly) provided that prevailing conditions permit. If an elevated hydrogen concentration persists, expert assistance may be required.
Experience has shown that measurement of gas concentrations during period of active ventilation may lead to unreliable results, particularly if the remote sensing hose of the gas detector is inserted into the hold within a stream of intake air or expelled gases. Care therefore needs to be taken when measuring gases during ventilation, which might be indicative only. Accurate gas readings might only be possible once ventilation has stopped, even if only for a short period of say a few tens of minutes.
In the event of a breakdown in mechanical ventilation, continuous natural ventilation can be applied until the mechanical fans can be restored. Weather conditions will need to be considered of course, and the frequency of monitoring hydrogen concentration and cargo temperatures should be increased.
If cargo temperatures increase above 65 °C, the Code calls for increased mechanical and natural ventilation to dissipate heat and any hydrogen, and to increase the frequency of gas and temperature measurements. It precludes the use of CO2, water or steam on the cargo, but does suggest bulkhead cooling if possible (e.g. spraying water from empty adjacent holds).
The Code does not set out the possible circumstances under which the cargo might exhibit elevated temperature, and clearly there might be issues with ventilating a cargo that is exhibiting heating due to reaction with air / oxygen. It might be appropriate in some circumstances to seek expert advice; any expert involvement would certainly have to include consideration of the full history of the cargo, including the logs of temperature and gas concentrations since loading.
Discharge
Hatch covers should only be opened if the hydrogen concentration in the ullage space of a hold has been determined to be below 1% by volume. Additional ventilation may therefore be required to achieve this threshold before discharge can commence.
A hydrogen concentration of 1% by volume is substantially below the lower flammability limit, giving a built-in safety margin. Moreover, the hydrogen content in the hold atmosphere will become increasingly diluted once the covers have been cracked open, adding a further safety margin.
As noted above, the Code allows for DRI (D) cargoes to be discharged during rain, but only if the entire complement of cargo within a hold is discharged at the same port, and not transshipped on to another vessel or leaving part of the (wet) cargo on board. If holds do need to be closed during periods of rain at the discharge port, the hydrogen concentration monitoring process will need to be restarted for those holds.
Summary
The IMSBC Code entry for DRI Type D differs substantially from the existing Type C entry: Both are for by-product fines, but the Type D entry recognizes the primary hazard of fines, which is hydrogen evolution due to reaction with water, rather than from self-heating via reaction with oxygen in air. The focus of the Code is therefore on the measurement and control of the hydrogen gas concentration by surface ventilation. This is unlike the other Code entries for DRI, where the basis for safety is the exclusion of both moisture and air.
Accordingly, Masters and crews will need to be appropriately trained in order to be prepared to contribute effectively to the assessment of the hydrogen evolution risk for a given voyage, with consideration of distances, speeds, the location of potential ports of refuge and weather conditions being factored in. In addition, a time-based gas prediction curve is plotted in order to estimate the length of time before the hydrogen concentration in each hold will reach the safety limit, this being 1% by volume, i.e. 25% LEL, and this data is then used to optimise a ventilation strategy. Typically, shippers would be expected to provide an expert cargo technician to assist with this process.
The cargo technician’s role is defined in more detail the Appendix to the schedule, and includes the following responsibilities:
- monitoring during loading operations and providing advice as appropriate;
- advising on and supervising the installation of the thermocouples for temperature measurement;
- monitoring and reporting on the cargo parameters (temperature and gas concentrations);
- assisting and advising the Master and crew in the development of the time-based gas prediction curve; and
- advising and coordinating with the Master and crew in connection with the operation of the ventilation system during the voyage.
Additional information can be found in the IIMA publication, ‘Direct Reduced Iron By-Product Fines (DRI D): A Guide to Handling, Storage & Shipping’ found on the IIMA website- www.metallics.org
All Clubs in the International Group have issued a similarly worded circular.

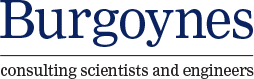
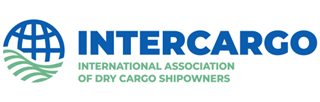