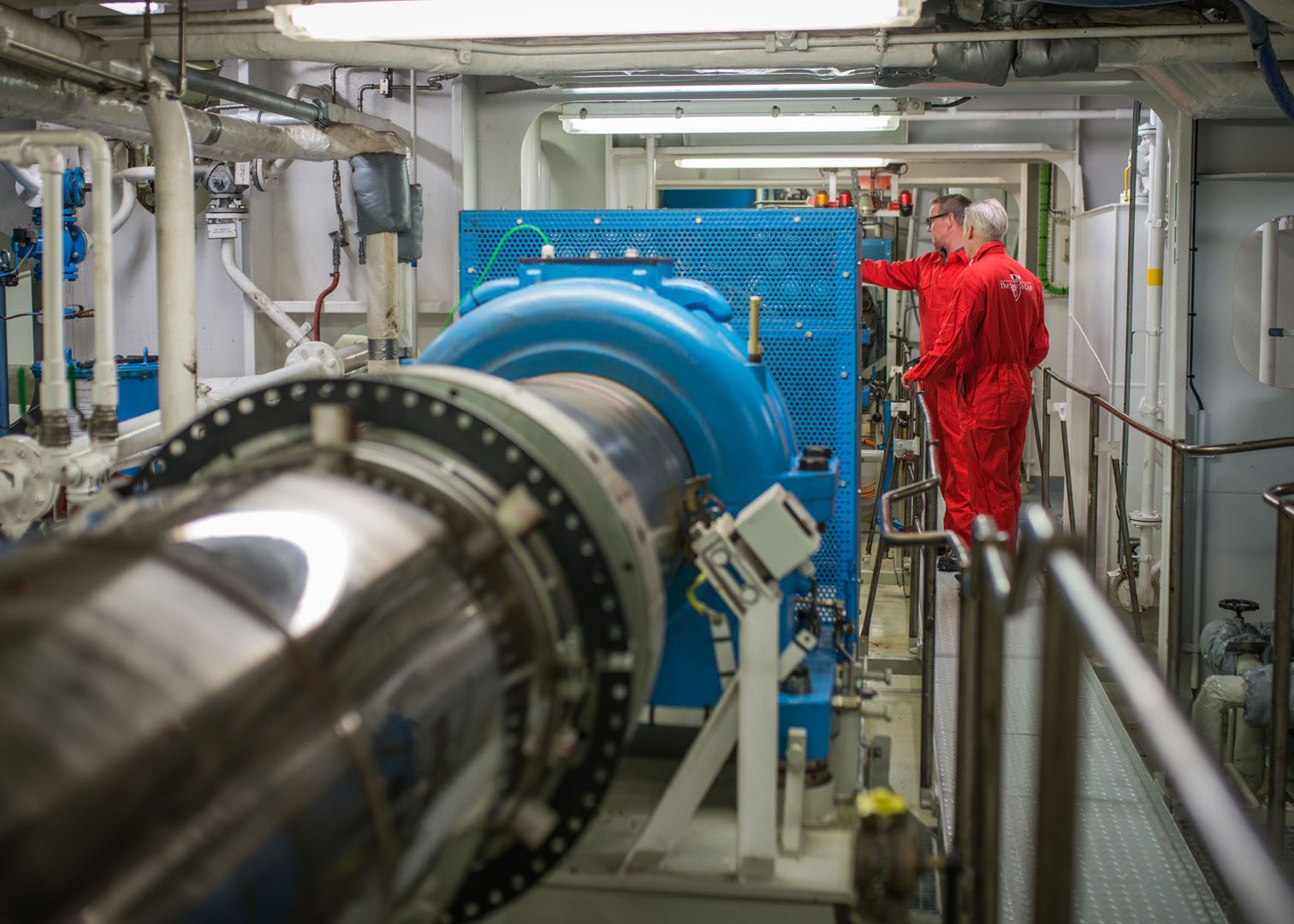
Machinery
Machinery claims are the most common claim type under H&M representing over 50% of all claims and 40% of costs. Below are some of the major causes, recurring issues and findings.
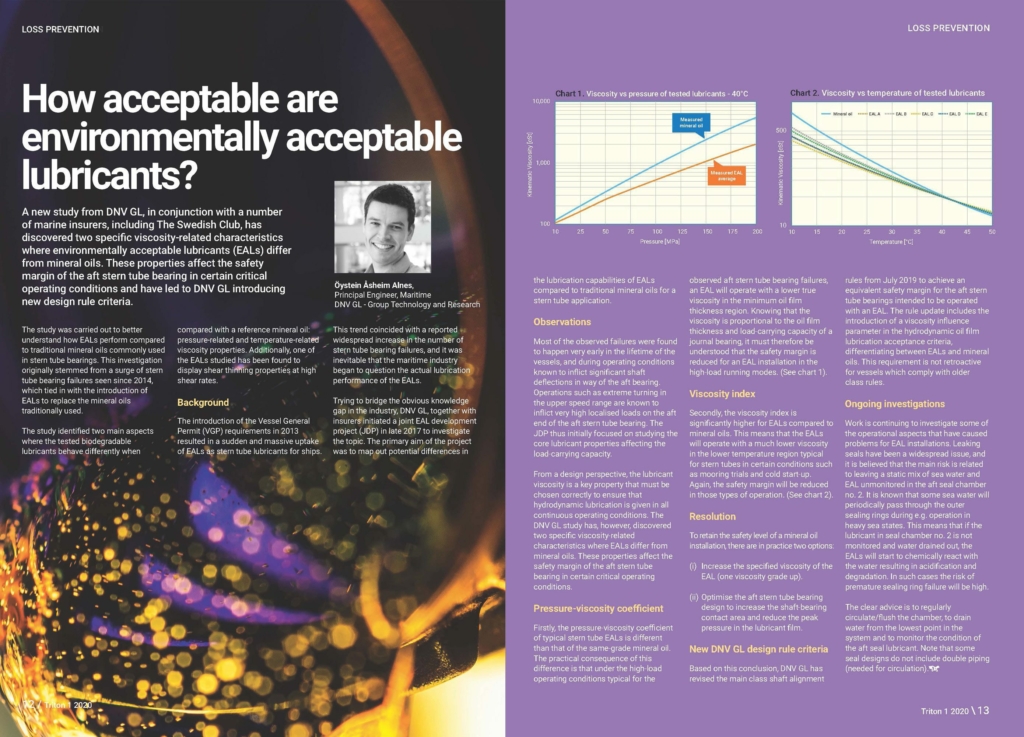
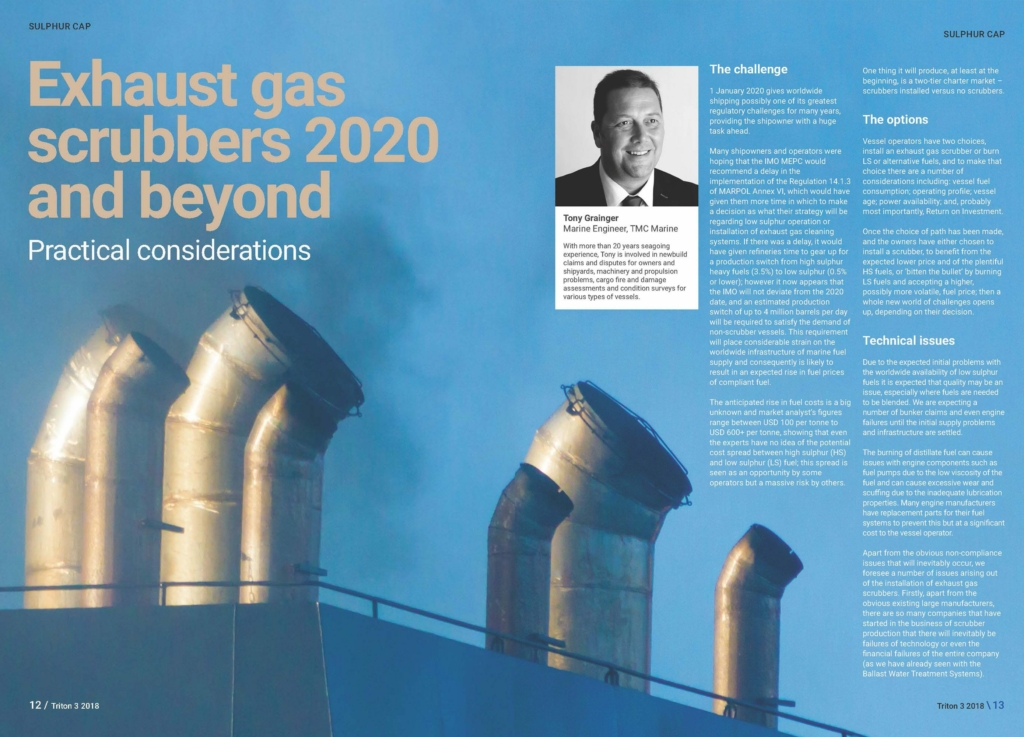
Scrubbers
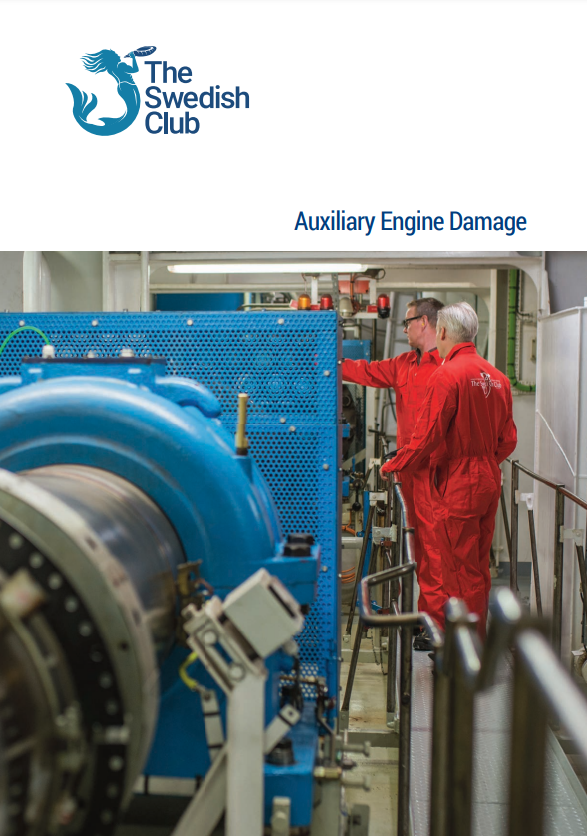
Auxiliary Engine Damage
The Auxiliary Engine Damage report has been created in response to members’ concerns over damage to auxiliary engines. Its objective is to investigate auxiliary engine claims, highlight predominating factors and provide advice with a view of reducing the frequency/severity of auxiliary engine damage. The Swedish Club has always had a proactive policy directed at raising awareness of claims trends and hands on advice on how to mitigate casualties. This report aims to shine a light on the important issue of damage to auxiliary engines, a significant segment of machinery claims – both in number and cost.
Major causes of damage
- Incorrect maintenance and repairs
- Failure to adhere to repair procedures and use of incorrect tools
- Crew lacking formal engine specific training
- Inexperienced crew and no expert in attendance
- Failure to detect contamination due to poor lubrication oil management
- Not following up on results from lubrication oil sampling
Time between overhaul (TBO)
The Club found that a majority of the casualties, 55%, occur within only 10% of the TBO, corresponding to the first 1,000 hours or so of operation after overhaul. In most cases, the damage occurs only a few hours after start up. The TBO of an auxiliary engine is normally between 12,000-16,000 hours.
Reviewing our records we note that the common factor for these occurrences in most cases is the incorrect assembly of vital engine parts in connection with regular overhaul. In particular, the assembly of connecting rods, bearings and pistons causes severe and costly accidents.
How to avoid auxiliary engine damage
- Ensure you have the necessary knowledge and experience before commencing any overhaul work.
- If you have not received training on the specific engine model, engage an expert from the manufacturer.
- Always strictly follow manufacturer’s instructions.
- During overhaul, check and double check that stud bolts for connection rods and bearing keeps are tightened 100% in accordance with manufacturer’s instructions.
- Ensure that required tools are available and calibrated as necessary.
- Monitor the quality of your lubrication oil and take prompt action when irregularities are detected.
Main engine damage
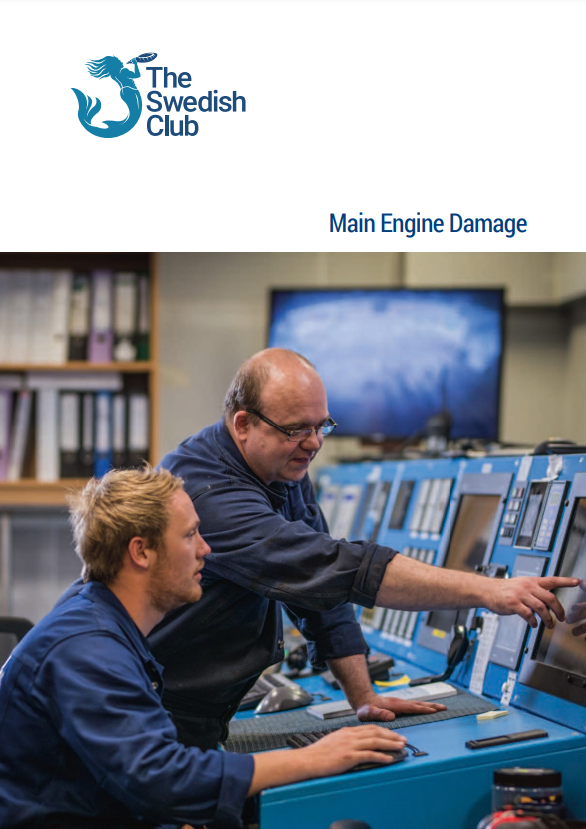
Main Engine Damage
This Main Engine Damage report from The Swedish Club, sheds light on an expensive category of damage that is all too frequent. Statistically a vessel will suffer between one and two incidences of main engine damage during its lifetime. Considering the costly consequences for ship owners and their hull insurers, it is important to identify the main causes of this damage and examine how these can be prevented. Initially the study aims to put main engine damage claims into context by examining claims statistics for the Hull and Machinery (H&M) segment. It then examines in detail main engine damage claims – specifically frequency, vessel type, engine manufacturer, engine speed, damaged parts and cause of damage.
Major findings
- The Club experienced 734 machinery claims in the 2015-2017 period, totalling USD 384 million. Main engine damage is the most expensive category with a total cost of USD 131 million, contributing to 16% of the cost of all H&M claims and 34% of all machinery claims.
- The average cost of main engine claims has increased by 21% since the period 2010-2014, amounting to almost USD 650,000 per claim. It should be noted that this increase in costs has, however, been seen across the board in all machinery claims.
- Costly rudder and bearing damage have affected the result for steering claims, which have seen an increase in cost of 53%.
- The increase in the average deck equipment claims cost is because the number of offshore vessels that the Club insures has increased during the period 2015-2017. These carry expensive deck equipment. As the proportion of offshore vessels in the Club’s portfolio increases, so does the average cost of deck equipment claims overall.
- On a positive note, the average claims cost for damaged turbochargers is reducing, a trend that has been apparent since the last publication. There has been a suggestion that a major contributing factor to this trend is the move seen in recent years from ball bearings to sliding bearings in the turbine rotor shafts.
- Medium/high speed engines are 2.5 times more frequently damaged than slow speed engines. They also have a disproportionate claims cost (43%) in relation to insured vessels (28%), whereas slow speed engines carry 72% of the insured vessels and 57% of the claims costs.
- Almost 60% of all insured vessels during the period of 2015-2017 were running on a slow speed S2 engine. They account for merely 30% of the claims and have a frequency of 0.012 claims per vessel. It is the best performing type of engine in the insured fleet.
- Generally speaking slow engines are more robust and have a lower damage frequency than medium/high speed engines.
- The medium/high speed engines are a minority in The Swedish Club’s insured fleet. The top three engine manufacturers account for 31% of all the costs in the fleet and 19% of all the insured vessels.
How to avoid main engine damage
Prevention of damage is naturally preferable to cure. A first step to avoiding damage is to have a wellimplemented and proper management system. This implementation can only be assured with proper training and education for the crew and providing them with the essential knowledge and experience required for ordinary daily work and maintenance according to company procedures.
- Implement robust onboard fuel and lubrication oil management systems.
- Carry out drip sampling when bunkering. Avoid consuming the fuel until analysis results are available.
- In addition to onboard testing of lubrication oil, submit samples for laboratory analysis at regular intervals,
at least every third month. - At regular intervals, carry out system checks of purifiers and filters for both fuel and lubrication oil systems.
- Ensure that maintenance manuals are at hand and that proper tools are available and calibrated. Crew members must have the necessary training and experience to carry out maintenance.
- It is highly recommended that engine maintenance is carried out as part of a computer based PMS (Planned Maintenance System), linked with the onshore organisation.
- During major overhauls it is recommended that an expert from the manufacturer is in attendance – consider a formal service agreement.
- Always take engine alarms seriously, for example oil mist detection, and investigate thoroughly. A fully functional alarm system is essential for the safe operation of the main engine.